
How Komet® Diamond Burs Are Made
Komet's Diamond Manufacturing: A Century of Excellence
Previously published on the Komet USA blog.
The Diamond Journey Begins
Ever wondered how Komet's diamond burs come to life? Let's take a closer look at this fascinating process:
1. Crafting the Diamond Blank
Our journey begins with the creation of the diamond blank on a CNC Turning Lathe. At this stage, no diamond particles are present, just a blank canvas.
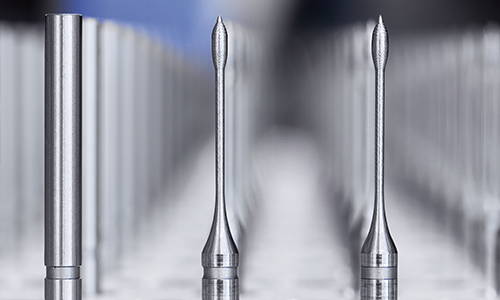
2. Ultrasonic Cleaning
Subsequently, the blanks undergo their first of several ultrasonic cleaning cycles. This meticulous process ensures that all foreign materials are removed, setting the stage for exceptional diamond performance.
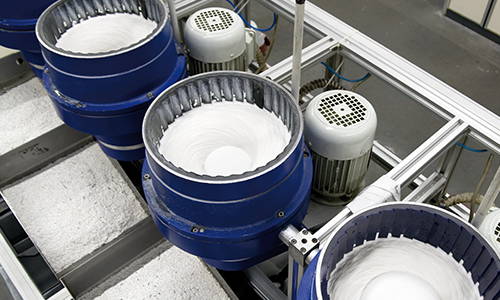
3. Precise Isolation
Precise isolation techniques are employed to shield specific areas where diamond particles should not be present. Precision is Komet's mantra.
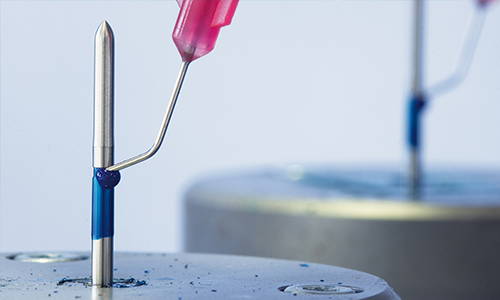
4. Coating
The blanks take a dip in a chemical bath known as Galvanic Bonding, creating a vital bonding layer for the diamond particles. Following this, they are immersed in the diamond bath, where the transformation truly begins.
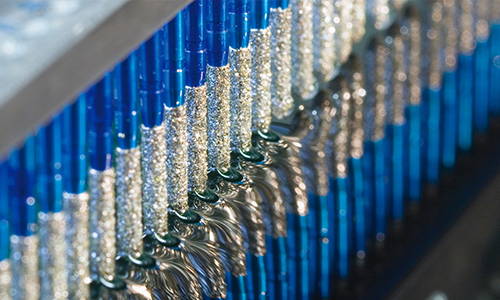
5. Colour Coding for Clarity
Komet's diamond burs are meticulously colour-coded according to their grit. For a deeper understanding, read the comprehensive colour-coding guide.
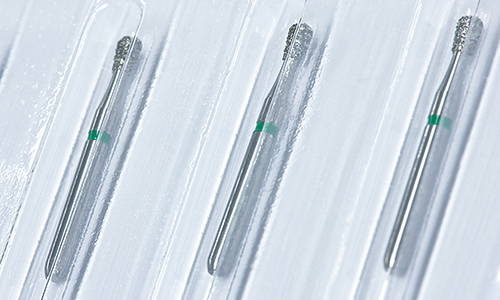
6. Optional Shank Coating
When required, some diamond burs undergo shank coating, achieved through immersion in a bath, resulting in a distinct shank color.
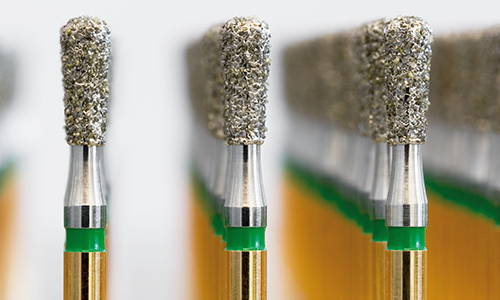
7. Final Ultrasonic Cleaning
A final ultrasonic cleaning process ensures the removal of any lingering debris, leaving Komet diamond burs in pristine condition.
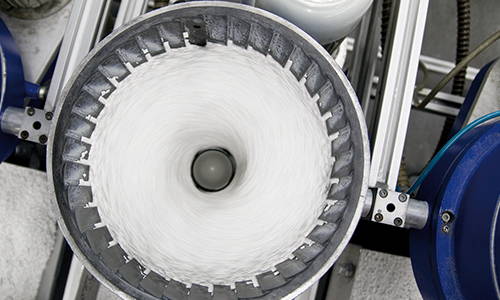
8. Quality Assurance
Each production batch undergoes rigorous quality assessments, a testament to Komet's unwavering commitment to high-quality standards.
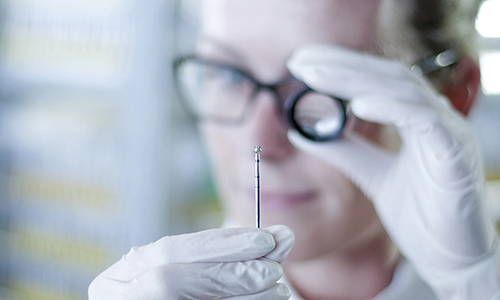
9. Secure and Sterilized Packaging
Komet burs are securely packaged under controlled cleanroom conditions. Following this, they undergo sterilization, rendering them ready for immediate use in your practice.
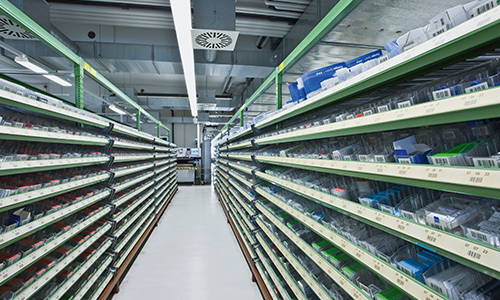
These meticulous steps ensure that every Komet diamond bur functions as a perfectly concentric cutting instrument, delivering optimal performance with every use. Trust Komet for quality, transparency, and precision in diamond manufacturing. Your patients deserve nothing less.